|
Most of our products are made by injection molding of GPPS (As described below)
which has crystal appearance similar to Acrylic but with cheaper price.
General Purpose Polystyrene (GPPS)
General Purpose Polystyrene, the parent of the styrene plastics family, is a
high-molecular-weight linear polymer consisting of about 2000-3000 styrene units.
General-purpose polystyrene (g.-p, ps) is often called crystal ps-the name denotes
only the clarity of the resin and should not be mistaken for crystallinity.
Property
The commercial success of crystal PS is owed to its clear advantages as a material.
It is easily formed into finished products that need little maintenance; is
light, versatile, and has excellent thermal and electrical properties. Much
of its advantage over other thermoplastics stems from its amorphous nature,
which results in clarity and fabrication ease. Because there is no crystalline
melting point, it needs little energy input and removal for fabrication (no
heat of crystallization), and the transition from glass to viscous liquid is
gradual. Above the glass transition temperature (Tg), PS is a viscous liquid
with high melt strength that can he fabricated easily by extrusion or injection
molding with little or no degradation.
Injection molding
The injection molding of thermoplastics is a process by which the plastic material
is melted and then injected into a mold cavity. Once the melted plastic is in
the mold. it cools to a shape that reflects the cavity.
The resulting form usually is a finished part, needing no other work before
assembly into or use as a finished product. Many details, such as bosses, ribs
and screw threads can be formed during the one-step injection molding operation.
An injection molding machine (as per figure shown) has
two basic components: an injection unit to melt and transfer the plastic
into the mold, and a clamp unit
1 ) to hold the mold shut against injection pressures and 2) for parts
removal.
|
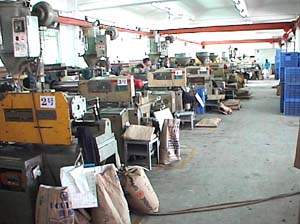
Injection Molding Department
|
The injection unit melts the plastic before it is injected into the mold, then
injects the melt with controlled pressure and rate into the mold.
|
|
|
|  | | Copyright 2004-2025 Tak Po Manufactory Ltd All rights reserved. |
|